We all know that the major impediment to production is failure of equipment in the process line. surely this is a no brainer. But did you know that the major cause of failure of any equipment ( at least mechanical) is Lubrication. Surprised !! you should be.
The Single Largest cause of failures in Mechanical moving equipments is Lubrication. Not the Lack of it, BUT WHEN YOU OVER LUBRICATE
More is not good. Not to humans, not to machines. Over Lubrication of machines can cause immense damage to the moving parts of the machines. Over Lubricaiton generates unwanted side effects like, excess heat, contamination of surroundings , and most of it all, the lubricants are not cheap, they cost. However the biggest cost is the breakdowns due to over lubrication.
Dual line systems and internal Leakages
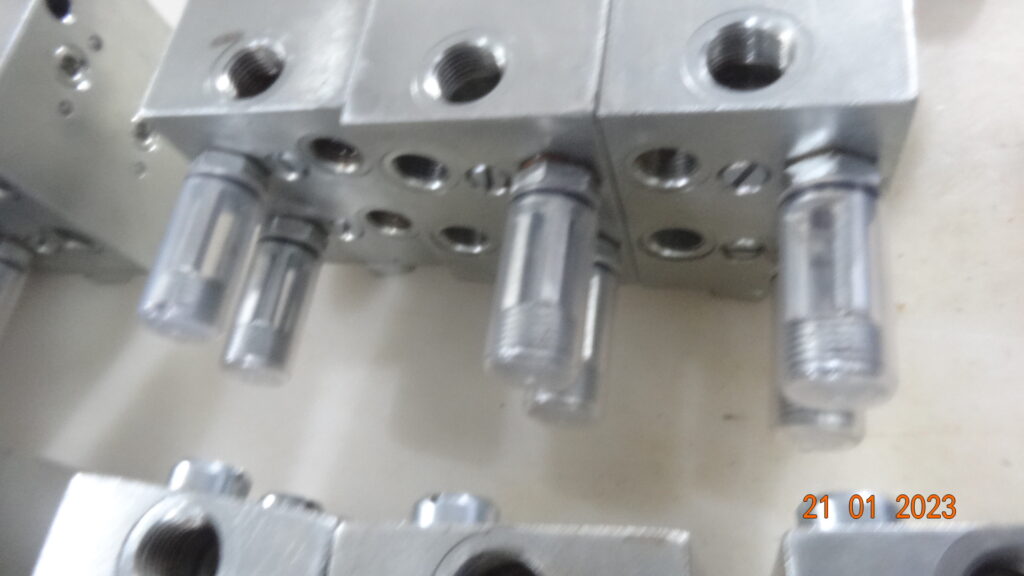
There is a co relation between the cracking pressure and the internal leakage in a metering device. The cracking pressure (the pressure at which the metering piston in inside the distributor starts moving ) is a function of the clearance between the piston and the bore . It is a metal to metal contact . When system pressures are more then 150 Bar ( which usually they are ) the problems start cropping due to internal leakages up based on the system length, operating pressure and few other factors which we will discuss later.
The internal leakages are never monitored in a Lubrication system. After all they are internal! They come to attention only when the system cycles are found to be inadequate or frequent failure of the pump elements. This results in the change of the pump , repair etc. But the underlying problem that may have caused it , is left un-addressed as this is an area that has been largely ignored.
The failure of the lube system occurs again and the process repeats. The maintenance costs keep going up. None the wiser .
There are ways aand means to avoid this . From the system design stage onwards, we can increase the efficiency of the lube system to minimise internal leakages. The manufacturing process of the Valves can be controlled and integrated with the system design to ensure that the cracking pressures are designed to suit a particular system. Letting go of the one shoe fits all philosophy, one can customise the distributors to suit a particular system, thus avoiding internal leakages, wastage of lubricant, increasing system integrity and minimizing not only system breakdown, but main machinery break down.
A WordPress Commenter
Hi, this is a comment.
To get started with moderating, editing, and deleting comments, please visit the Comments screen in the dashboard.
Commenter avatars come from Gravatar.